Process Improvement and Innovation
By David Spak
Definition is the first step in Process Improvement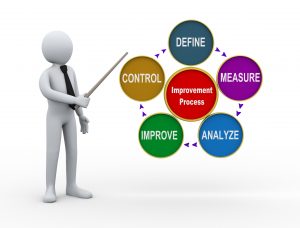
Ask someone about process improvement or continuous improvement and you will likely receive a combination of blank stares and ambiguous definitions. Ask an expert about these terms and you will likely be inundated with industry buzzwords like six sigma, lean, and kaizen. Yet if you step back and break the term process improvement into its component parts, you will see that in order to pursue process improvement you need two things:
- A process.
- A desire for improvement.
The first part of the phrase – process – is in many cases the element that trips up individuals and/or organizations. A process is a set of definable tasks ordered towards an outcome. Brushing your teeth is a process. So is making breakfast. There is a process for building a car from scratch, and for putting gas in the used car in your driveway.
All of these processes can be mapped out, and, depending on interest, need, or profitability, improved. Therefore the first step in process improvement is simply identifying and defining your process(es), and then determining that you’d like to improve them.
What happens next is also significant. Specifically, how would you like to improve your processes? Let’s say you own a construction company and build houses. You can outline your processes and decide that you want to improve them, focusing on reductions in work time, cost of materials, and emergency expenses related to on the job injuries. Applying a traditional process improvement methodology might result in a 10-20% increase in annual profitability, which makes you very happy.
But what if you don’t want to increase your annual profit from, say, $750,000 to $1,000,000? What if you want to own a $100m construction company? Suddenly you are less focused on process improvement and more focused on innovation. This tension in the second step of process improvement – how an organization improves – is the basis of a Forbes opinion piece by Alastair Dryburgh .
“Some very successful companies became that way without practicing continuous improvement. Consider Microsoft, for example. They didn’t launch Windows 95 and just keep improving it…every couple of years they launched something new with a new set of features and a new set of bugs”.
The point that Drybaugh is making is an important one, and not because he assumes that continuous/process improvement is an obsolete business practice. “I’m not arguing against continuous improvement in itself”, he writes. “I’m arguing against it as a substitute for innovation or original thinking”. This distinction is a key component of determining how to improve a process. In some cases steady, marginal improvement is both desirable and attainable. In other cases it is short-sighted and reactionary.
These concepts apply to both public and private sector organizations. In the federal government, for example, there is a well-defined process associated with the review and application of environmental policy. Federal agencies can and do use the principles of process improvement to increase efficiency in environmental reviews, thereby expediting services to individual citizens while also abiding by the regulations of the National Environmental Policy Act (NEPA).
In state and local governments, the use of speed cameras has proven to be both a source of revenue and a way to reduce traffic accidents. By adopting a technological innovation, local governments throughout the United States have improved public safety while accessing a steady and predictable revenue stream.
So how to choose between steady process improvement and a complete reordering towards innovation? This decision is ultimately rooted in technical skill – who has the ability to create a truly innovative product? But the final decision is balanced by government regulation, industry practices, and personal values. In the end it is important to both define the process you are trying to improve, and understand the best method for sustainable, long-term improvement.